SAPEC AFRICA
(PTY) LTD
SPECIALISES IN THE PREVENTION OF FIRESIDE FOULING IN INDUSTRIAL BOILERS AND WASTE HEAT RECOVERY PLANT
Our Services
Combustion catalysts
Coal and ash analyses and quality monitoring
Coal sourcing
Coal and combustion training courses
Boiler efficiency surveys and recommendations
Why SAPEC?
- REDUCE BOILER FOULING AND SLAGGING
- IMPROVE EFFICIENCY AND SAVE FUEL
- REDUCE EMISSIONS
- REDUCE DOWNTIME AND CLEANING COSTS
We care about the environment, to have any impact on climate change the world’s finite fuel resources must be used more efficiently.
SAPEC INDUSTRIAL CHEMICALS LTD is a UK-based company that specialize in combustion and boiler fireside treatment programmes for boilers and incinerators.
SAPEC AFRICA(PTY) LTD exclusively markets SAPEC products throughout Africa and is part of a global network of companies that now offer SAPEC fireside treatment products. SAPEC AFRICA is combustion and coal specialists and can offer additional services all aimed at improving boiler performance and efficiency and reducing emissions. These services include Boiler Consultancy. Coal and ash analysis and boiler operator training.
The SAPEC 523 treatment was developed by Len Hardy in the early 1980’s. The subject of boiler fouling is extremely complicated.
Fire‑side fouling is caused by the formation of heat resistant, bonded deposits on the heat transfer surfaces of the boiler reduce the heat transfer rate. The boiler must then operate for longer periods to restore the system to equilibrium, thereby using excess fuel and producing more CO2 for the same loading.
However, due to the costs of fouling there was a need for a solution. The original fuel additives developed in the 1950’s, 60’s and 70’s earned considerable criticism much of it is entirely justified. Many of the products offered were placebo products and therefore in such a difficult market, where scepticism is the order of the day, it was essential for Len to prove that the SAPEC treatment could be different. A major factor in the research and development of the SAPEC was the work carried out with two British tobacco companies. They were able to prove that SAPEC was able to reduce the tar and particulate matter produced from tobacco. These controlled trials gave a degree of testing and accuracy that would not have been possible in boiler trials, what is more, they backed up Len’s original theory and enabled him to proceed to the next phase, proving the product in the field with real boilers and real problems. In the early stages, this entailed providing free trials with the SAPEC System, sometimes over long periods and at a considerable cost.
As a result of all the work SAPEC 523 treatment has now been established globally and across the whole spectrum of boiler type and size. Because of its unique chemical reaction, it can work effectively with many different fuels such as coal/oil/waste/ biomass.
Years IN THE UNITED KINGDOM
YEARS IN SOUTH AFRICA
Years IN THE ASIAN PACIFIC
YEARS IN EUROPE
What We Do
Sapec 523 treatment reduces the soots/tar produced from burning Fossil Fuel, Biomass, Waste and Furnace Oils. It effectively removes the “glue effect” for potential Fireside fouling which would normally reduce the heat transfer coefficient. Sapec 523 treatment denatures deposits and keeps them soft and free-flowing, reducing the need mechanical cleaning, thereby protecting the metal. The reduction in fouling leads to more efficient operation for prolonged periods. Operating times can in some cases be doubled. Allowing for more boiler availability. Sapec 523 treatment is effectively a combustion availability extension tool.
Sapec 523 treatment is a catalyst, releasing onset energy of combustion at a lower temperature, therefore reducing loss of energy via the Stack. SAPEC 523 creates a reducing atmosphere in combustion conditions. More Carbon Monoxide and Oxygen is used in the combustion process, and there is a significant reduction in emissions of PM (particulate matter),
Stack emissions are visibly cleaner and there is a reduction in carbon in the boiler solids and the boiler ash. Cleaner heat transfer surfaces lead to fuel savings. A 5 % minimum reduction in coal is commonplace and has been proven extensively in wide variety applications, with 3rd party auditing.
Sapec 523 treatment is inert, therefore does not get consumed in reaction, and does not get entrained in flue gas pass, and is fully environmentally friendly with regards to disposal, landfill, brickmaking and contact with effluent water.
Application and dosing is relatively simple, and easily monitorable.
Sapec 523
Combustion catalyst application versatility
Fossil Fuel
Chemical remains of prehistoric plants and animals
- Lignite Coal
- Bituminous Coal
- Subbituminous Coal
- Anthracite
Biomass
Plant or animal material used as fuel to produce electricity or heat
- Straw
- Bagasse
- Husks
- Wood
- Peels
- Pulp
- Shells ( PKS)
- Stalks / Kernels
Hydrocarbon
Organic compound consisting of Hydrogen and carbon
- Heavy Furnace Oil
- Natural gas
- Coal
Incineration
Reduces dioxin formation that is inevitable when you incinerate waste
- Organic and
- Inorganic waste
SAPEC
Specialist additives for pollution and efficiency control
HOW WE DO IT
Are divided into 3 parts for a successful chemical solution for a chemical problem
Part 1: Product
SAPEC 523 treatment is supplied as a granular powder. It is a unique fuel treatment that is equally effective at reducing fireside deposits in coal, heavy fuel oil, waste incineration and other fossil fuels.
SAPEC 523 is injected directly into the combustion zone. The treatment is catalytic in action and solely confined to the combustion zone. The dosage required is very small at approximately 200g per ton of coal. SAPEC prevents the initial adhesion of the deposits to the boiler heat transfer surfaces. By preventing this initial stage of deposition, SAPEC 523 treatment prevents the formation of hard bonded deposits, any subsequent deposits will be soft and easily removed without the need for mechanical de-scaling. Soot/tar deposits are eliminated in the boiler solids and stack emissions.
HEALTH AND SAFETY
The SAPEC 523 treatment is non-flammable, non-volatile and non-toxic and is completely safe to use. As part of our commitment to safety, we ensure that our product SDS’s are comprehensive, transparent and compliant as per agreed 16 section format for our clients.
Fire-tube boiler without any treatment-6 months operation

The same fire-tube boiler after 6 months operation with SAPEC 523 treatment

Part 2: Product KL injection/feeder machines
KL-SERIES INJECTION/FEEDER MACHINES
-
- Fully automatic
- Consistent and accurate dosage
- 90kg to 250 kg capacity of treatment
- Can inject into pressurized systems
- Removable timer compartment for easy maintenance
- 220-240 / 110-volt machines available
- 1-2 bar dry compressed air required
- Quick and easy installation
The KL-SERIES Automatic feeder is designed to inject powder as an airborne dust into the combustion chamber. The pneumatic delivery system will provide a constant dose rate of treatment. Electronic timing units give an extensive time range, allowing the KL-SERIES to dose accurately across the whole spectrum of boiler plant.
Boiler fouling is a continuous process that is directly determined by the amount of fuel burnt. The flexibility of the SAPEC feeders allows us to ensure that the SAPEC treatment is always present in the combustion zone, where it can be effective. In a typical installation, the treatment is injected into the boiler at 3-to-15-minute intervals thereby making the SAPEC addition a continuous process also. The unit is free-standing and can inject into pressures of up to 72 inches WG. Normally floor mounted it can deliver the treatment to a height of 40 ft. The KL-Injection machines are manufactured under license in South Africa.





Part 3: Product Service
SERVICE IS THE KEY TO SUCCESS
Ultimately if the SAPEC 523 treatment does not get into the boiler then it cannot achieve results.
The injection machines have been designed to require little maintenance and are very reliable. However, boiler houses are often inhospitable environments, Feeders can often get sprayed with water, covered in dust or simply switched off by boiler personnel or through power failures in the boiler house.
SAPEC employs service operators to look after the operation of the feeders. The service operator can regularly visit customers within their region to check the injectors and fill them where necessary. This allows SAPEC complete control over the dosage rates and machines, therefore allowing us to guarantee the results.
Regular service visits allow us to ensure continuity of supply and allow problems to be quickly solved. Whenever we start with a customer, we invariably start the system on one boiler. The duration of the trial usually mirrors the normal operating time between boiler cleans. If we don’t identify dosage problems quickly then months may be wasted and the whole trial, as well as our reputation, is then at risk.
The KL-series Feeder machines are designed for easy maintenance. The service operators carry interchangeable parts and do not need any special skills; therefore, they offer a very cost-effective method of covering large areas and are able to ensure that the feeder machines are working and that the SAPEC system is providing a benefit to customers.
SAPEC – A Brief History
The first SAPEC fuel treatment was launched in 1985. The product was invented in the UK by Mr Len Hardy. Len who was 61 at the time and a fellow of the Institute of Mechanical Engineers had spent most of his working life involved at senior levels in Power stations and energy related businesses. For the previous 5 years he had been an independent consultant working with British Coal amongst others on fouling problems in coal fired boilers, during this time he worked with several coal additives.
One of our Business Partners
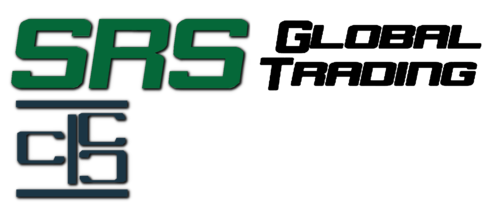
GET IN TOUCH WITH US!

Stay informed on Covid-19: Visit the SA Dept of Health Online Portal HERE